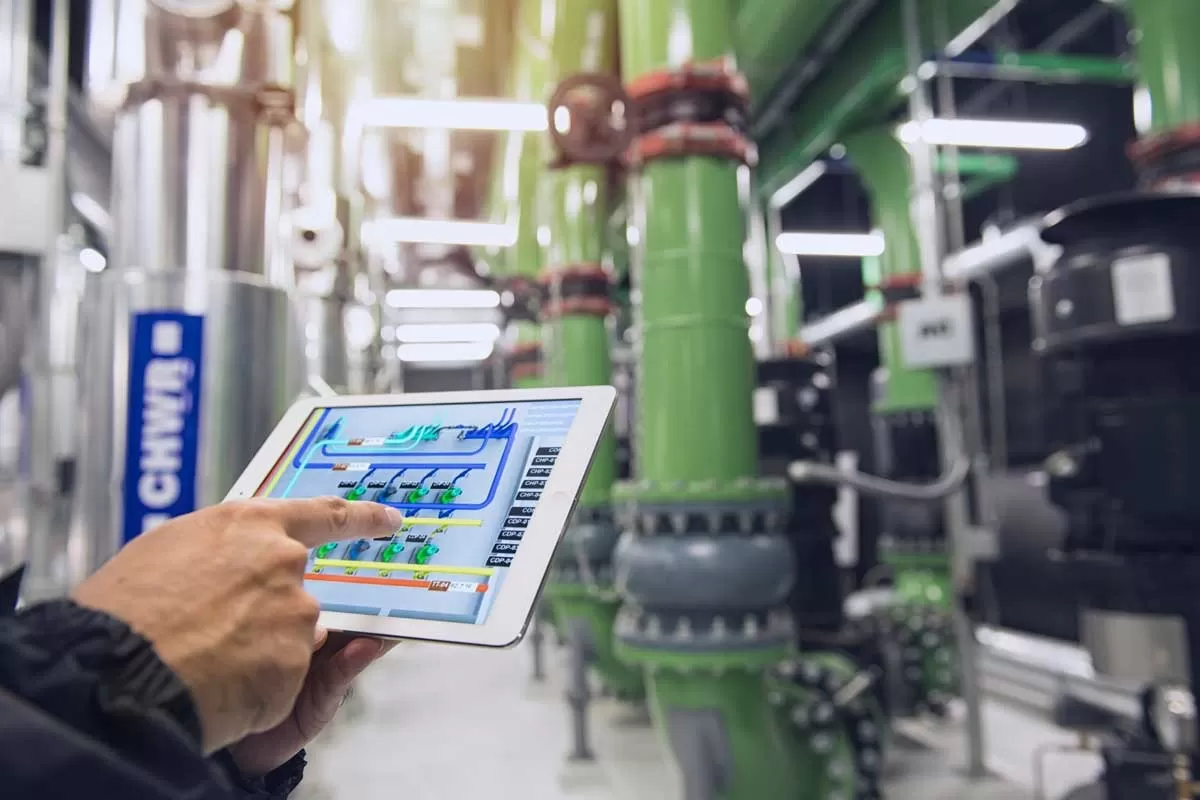
The Benefits of Predictive Maintenance for Commercial HVAC Systems
Introduction:
For commercial buildings, HVAC systems are critical to maintaining a comfortable, safe, and productive environment. However, traditional reactive or time-based maintenance strategies often lead to unexpected failures, costly repairs, and inefficient energy usage. Enter predictive maintenance — a proactive approach that uses data and technology to detect potential issues before they turn into major problems. In this blog, we’ll explore the key benefits of predictive maintenance for commercial HVAC systems and why it’s becoming a must-have for modern facilities.
What Is Predictive Maintenance?
Predictive maintenance involves the use of sensors, data analytics, and real-time monitoring to assess the performance and condition of HVAC systems. Instead of waiting for something to go wrong or scheduling maintenance based solely on time intervals, predictive maintenance allows building managers to take action based on actual equipment data and performance trends.
Key Benefits of Predictive Maintenance for Commercial HVAC
1. Reduced Downtime and Disruptions
HVAC failures in commercial buildings can disrupt operations, make tenants uncomfortable, and even force business closures. Predictive maintenance detects early signs of wear or malfunction, allowing you to fix issues before they result in complete system breakdowns.
Benefit: Increased reliability and fewer interruptions to business operations.
2. Lower Repair Costs
When minor issues are identified early, they can be resolved before escalating into major, costly repairs. Predictive maintenance helps catch problems such as clogged filters, refrigerant leaks, or failing components before they lead to expensive damage.
Example: Replacing a worn fan belt costs significantly less than dealing with motor failure caused by neglect.
3. Extended Equipment Lifespan
Regular monitoring and timely intervention prevent unnecessary stress on HVAC components. This can significantly extend the life of your HVAC system, delaying the need for costly replacements.
Insight: Systems that undergo predictive maintenance tend to have 20–40% longer lifespans compared to those maintained reactively.
4. Enhanced Energy Efficiency
Predictive maintenance ensures that your HVAC system runs at peak efficiency. Dirty coils, blocked airflow, and malfunctioning thermostats often go unnoticed but can drastically increase energy consumption.
Result: Lower utility bills and reduced environmental impact due to optimal system performance.
5. Improved Indoor Air Quality and Comfort
Malfunctioning HVAC systems can lead to poor air circulation, humidity issues, and inconsistent temperatures. Predictive maintenance helps maintain a comfortable and healthy indoor environment by ensuring every component functions as intended.
Benefit: Better occupant satisfaction, especially in office buildings, schools, and healthcare facilities.
6. Data-Driven Decision Making
With the insights provided by HVAC sensors and analytics platforms, facility managers can make smarter, data-driven decisions regarding maintenance schedules, system upgrades, and energy usage.
Bonus: Reports and alerts help track trends, identify recurring issues, and justify budget allocations.
7. Regulatory Compliance and Safety
For many industries, HVAC performance is tied to health and safety compliance standards. Predictive maintenance helps ensure your system meets required guidelines and reduces the risk of non-compliance penalties.
Key Areas: Air quality standards, temperature control for sensitive goods, and workplace comfort regulations.
8. Cost Predictability and Budget Control
Predictive maintenance shifts HVAC care from unpredictable emergency repairs to planned, manageable upkeep. This allows facility managers to better control maintenance budgets and avoid unexpected financial hits.
Advantage: Easier forecasting and long-term financial planning.
How to Implement Predictive Maintenance
To successfully implement predictive maintenance, consider the following steps:
- Install Smart Sensors: Monitor temperature, humidity, pressure, vibration, and more.
- Use Building Management Systems (BMS): Centralize control and analysis of HVAC data.
- Partner with Experienced HVAC Technicians: Ensure proper setup and ongoing support.
- Train Your Staff: Educate building maintenance teams on using predictive tools effectively.
Conclusion:
Predictive maintenance is transforming how commercial facilities manage commercial HVAC systems. By shifting from reactive to proactive maintenance strategies, businesses can enjoy lower costs, improved efficiency, greater system longevity, and a healthier indoor environment. Investing in predictive maintenance isn’t just smart — it’s essential for staying ahead in today’s energy-conscious, cost-sensitive landscape.
Ready to make the switch to predictive maintenance?
Our HVAC experts can help you set up the right system to monitor, maintain, and maximize the performance of your commercial HVAC investment.